Les briques alimentaires constituent le principal emballage des jus et du lait. En effet, 52 % des jus de fruits vendus dans le commerce sont emballés dans des briques en carton, 38 % dans des bouteilles en plastique et 8,5 % dans des bouteilles en verre. Pour le lait, les briques représentent 55,5 % des ventes, le plastique 41,5 % et le verre 0,6 %. Intéressons-nous à la fabrication et au recyclage des briques Tetra Pak, leader de la brique alimentaire en France.
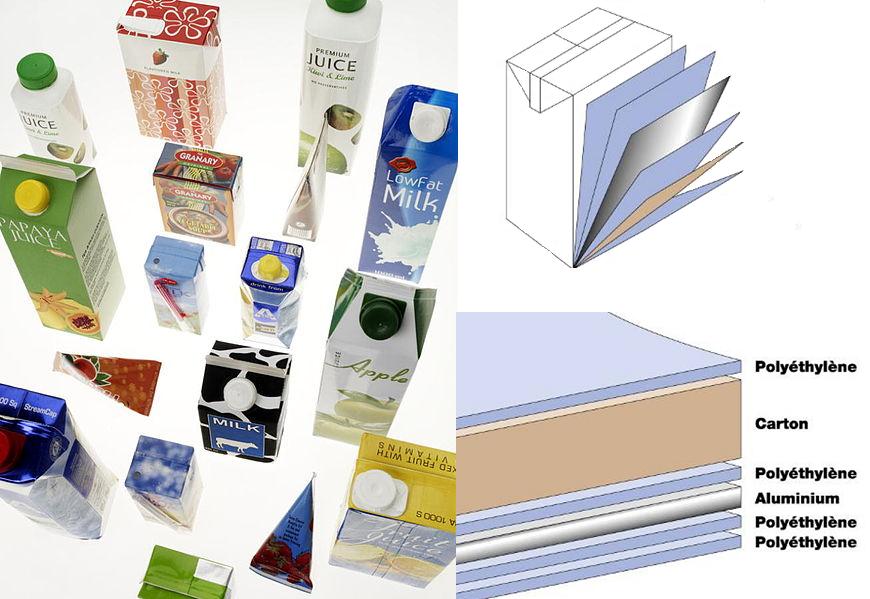
Les briques Tetra Pak sont constituées de carton, plastique et aluminium. Les différentes couches sont assemblées dans l’usine de Dijon en France pour au moins 60 % des emballages vendus en France. PHOTO//DR
Les briques Tetra Pak, c’est de 73 à 75 % de carton, de 20 à 23 % de polyéthylène et de 4 à 5 % d’aluminium. Leur composition varie légèrement selon la nature du produit, mais le seul matériau en contact avec le contenu est toujours un polyéthylène de « qualité alimentaire ». Le carton confère à l’emballage sa solidité et sa rigidité. Le plastique lui assure son étanchéité et protège les décors. Pour sa part, l’aluminium agit comme une barrière, protégeant le produit de la lumière et de l’oxygène.
D’où viennent les matières et les emballages ?
Au niveau mondial, 173 milliards d’emballages Tetra Pak ont été fabriqués en 2012 dans 170 pays. Proche de chez nous, 4,5 milliards de briques sont produites en Italie, 7,8 milliards en Espagne et au Portugal et 3,8 milliards à Dijon, en France. Sur le total des briques fabriquées à Dijon, environ 40 % sont vendues en France et 60 % partent à l’export. Les flux d’emballages entre les pays sont très variés, puisqu’ils dépendent des productions et des lieux de vente des clients. D’après les chiffres officiels de l’entreprise, il est tout de même possible de dire qu’au moins 60 % des emballages de Tetra Pak achetés en France sont produits à Dijon, le reste provenant principalement d’Espagne, d’Italie ou du Portugal.
Le carton des emballages Tetra Pak fabriqués en France provient de forêts scandinaves certifiées FSC. En France, 90 % du carton des emballages est certifié FSC, mais seulement 24 % des emballages sont porteurs du label. Pourquoi ? Tout simplement parce que les fabricants jugent que le label souffre encore de visibilité et prend trop de place sur l’emballage ! L’objectif de Tetra Pak est d’augmenter le pourcentage d’emballages porteurs du label en France à 50 % en 2015.
Les sources de polyéthylène et d’aluminium sont plus variées que celles du carton. Ces matières proviennent de différents pays d’Europe, dont la France, l’Espagne, les Pays-Bas, l’Allemagne et le Luxembourg.
Un recyclage en progression
45 % des briques jetées en France sont recyclées, l’objectif étant d’atteindre 50 % d’ici 2015. Après le tri par les consommateurs, les emballages sont traités dans le cadre de la collecte organisée par la filière REVIPAC et d’autres organismes (FNADE et FEDEREC), agréés par Eco-Emballages. Le recyclage se fait par séparation des matériaux par pulpage, notamment en France par la société SCA à Louviers (Eure) et chez le papetier Novatissue (Groupe Lucart) dans les Vosges. Une partie du recyclage s’effectue également en Espagne chez StoraEnso, à Barcelone.
Après pulpage, le carton est recyclé en essuie-tout et papiers d’essuyage, principalement par Novatissue. La partie PE-aluminium est recyclée en mobilier urbain et piquets de vigne par la société Traidib et en articles de bureau par la société Viquel.
Depuis 2004, 99,5 % des déchets solides (chutes d’aluminium et marges de polyéthylène) de l’usine de Dijon sont recyclés, les 0,5 % restant sont incinérés et valorisés énergétiquement.
Comment fabriquer une brique ?
Dans l’usine de Dijon, des bobines de carton d’environ 5 km de long sont acheminées par chemin de fer en provenance de Scandinavie. Chaque bobine de carton permet la production de 100 000 emballages de 1 litre. Le polyéthylène y est acheminé sous forme de granulés et l’aluminium en bobines, le tout par camions.
Dans l’usine de Dijon, Tetra Pak commence par imprimer sur le carton les décors de ses clients. Arrivé sous forme de granulés, le polyéthylène est fondu à 300°C et appliqué directement sur les deux faces du carton, sans colles. Vient alors s’ajouter une couche extrêmement fine d’aluminium à l’intérieur. Deux couches de polyéthylène sont finalement ajoutées sur l’aluminium pour assurer le contact alimentaire avec le produit.
Les emballages sont ensuite livrés aux clients sous forme de rouleaux de 2 tonnes. Ils n’auront plus qu’à les découper et les remplir de produits. Pour ce faire, le remplissage se fait de façon aseptique : le rouleau de matériau est d’abord stérilisé à plat avant de prendre sa forme cylindrique et d’être rempli en continu par le liquide, sans contact avec l’oxygène de l’air, puis soudé sous le niveau du liquide.
Remplacer le polyéthylène et l’aluminium ?
Du côté de l’empreinte écologique, une étude menée par Tetra Pak en 2008 portant sur le cycle de vie des emballages en verre, plastique et carton, donne un avantage net à la brique alimentaire. Mais l’entreprise veut améliorer ses résultats fabriquant un emballage produit exclusivement à base de ressources renouvelables.
Tetra Pak mène ainsi des recherches pour remplacer l’aluminium et le polyéthylène par un polymère basse densité à base de canne à sucre. L’entreprise propose déjà des bouchons en polymère haute densité dérivé de la canne à sucre, produit au Brésil par la société Braskem. Avec 610 millions de bouchons commercialisés dans le monde pour le moment (sur les 173 milliards d’emballages), Tetra Pak vise 100 % de ses emballages équipés. Ces bouchons devraient fermer une partie des emballages Français dès 2014.
Auteur : Matthieu Combe, fondateur du webzine Natura-sciences.com
Tetra pak protège ce qui est bon avec l’aluminium et le polyéthylène! &#é^%://
Vive le verre et la consigne!
A noter que le leader mondial des solutions de traitement et de conditionnement des produits alimentaires a basé son siège mondial, Tetra Laval, en suisse !!??